Posted: September 26, 2024
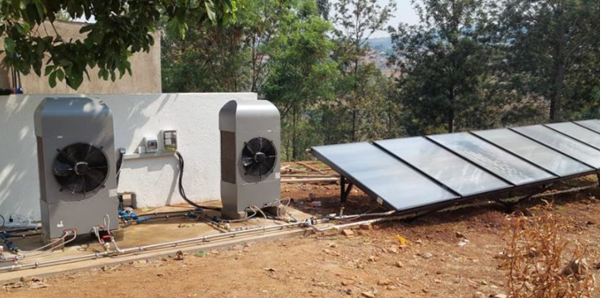
Photo: Purix
The future markets for solar thermal cooling systems are in the global south. The IEA study The Future of Cooling predicts that by 2050 37 % of total electricity demand growth will be for air conditioning. Solar thermal cooling systems have two major advantages. They consume up to a factor of five less electricity than compression chillers and use natural refrigerants. The challenge is now to standardize solar cooling kits for a mass market and adapt them to the constraints of the sunbelt regions. Researchers from the IEA SHC Task 65 on “Solar Cooling for the Sunbelt Regions” have put together a report with a number of standardized solar cooling kits highlighting sunbelt-specific adaptations. The photo shows an installation for a cold storage room in Rwanda. :
“Many manufacturers, solar system providers and researchers shared their valuable experiences and insights regarding standardization and the adaptation of cooling kits to the sunbelt regions with us by filling in surveys and taking part in personal interviews”, explained Dr. Monika Weiss, Chief Sustainability Officer of the US American company ergSol and one of the authors of the report. Under the title Standardized Solar Cooling Kits several products are introduced (see following table) and general findings on system adaptations are gathered.
Company, country
|
Type of solar cooling system
|
Product name (cooling load)
|
Solar sunbelt adaptation
|
SolarNext, Germany
|
Lithium bromide absorption chillers
|
Chilli cooling kit HL350ADB (384 kW)
|
Adapted condenser that is designed to operate at outdoor temperatures between 32 and 38 °C and adiabatic coil circuit cooling tower (closed system) to address the special environmental conditions
|
Purix, Denmark
|
Lithium bromide absorption chiller
|
Purix chiller A25s
(2.5 kW)
|
Technology widely applicable for sunny regions worldwide
|
ARES, Netherlands
|
Silica-gel adsorption chiller
|
SolabChiller (5 kW)
|
Ongoing R&D activities with universities in the sunbelt regions to evaluate performance and develop adaptation strategies
|
Fahrenheit, Germany
|
Silica-gel or zeolite adsorption chillers
|
eCoo 20
(20 kW)
Zeo M 29
(20 kW)
|
An adiabatic instead of a dry re-cooling system is capable of meeting the required cooling load despite high ambient temperatures
|
SolarInvent, Italy
|
Desiccant -evaporative systems
|
Freescoo VMC 3.0
(3.2 kW)
|
System adaptation to hot and/or humid conditions involves properly sizing the adsorbent and evaporative components.
|
Overview of market-ready products in different capacity ranges using various cooling technologies introduced in the IEA SHC Task 65 report Standardized Solar Cooling Kits
Findings on system adaptations in sunbelt regions
“We clearly see the trend in the market that small units with a capacity lower than 20 kW are getting more compact, thus having lower upfront costs and targeting the mass market”, said Dr Uli Jakob, who chairs IEA SHC Task 65. “We also see that heat-rejection systems in hot climates with temperatures regularly above 30 °C pose significant challenges.” In such high temperatures the solar cooling systems require a wet cooling tower, which is not a suitable component in many regions because of its high water need. Therefore, adiabatic coolers with pads or adiabatic cooling towers with a coil circuit (closed system) are the technical alternative for this challenge.
One of the lessons learned by the report’s authors is to “use medium-temperature solar systems to operate two-stage absorption chillers to increase competitiveness”. The SunBeltChiller concept developed by the German research institute ZAE Bayern demonstrates this. It is powered by concentrating solar collectors at temperatures higher than 160 °C. In the first step, the solar collectors drive a special absorption chiller called a double-lift machine which can be re-cooled at very high temperatures (approx. 90° C). In the second step, the waste heat from the double-lift machine drives a classic single-effect absorption cycle, which is re-cooled using the ambient temperature at night. The overall efficiency of these two steps is equivalent to a double-effect absorption chiller with a COP of 1.35, according to the authors of the report.
Another lesson learned from the stakeholder interviews is the necessity and frequency of cleaning concentrating collectors. Dust contamination on the mirrors can reduce performance by approximately 1 % per day in the dry season (worst case), leading to a typical performance loss of 20 % per month. The objective is to clean the collector every 14 days, resulting in an average performance loss of 5% within this timeframe. Cleaning methods include high-pressure cleaners or manually cleaning the mirror surface and using a window squeegee to dry it.
Task 65 came to an end in June this year. All publications from the four-year research platform are available for download here: https://task65.iea-shc.org/publications
Organizations mentioned in this news article: